STORIA ED EVOLUZIONE DEL SISTEMA COMMON RAIL
Sebbene sia divenuto famoso con il suo nome inglese, Common Rail, il sistema di alimentazione Diesel a condotto comune o collettore comune, che dir si voglia, fu inventato dal fisico italiano Mario Ricco, al quale è stata conferita la laurea magistrale ad honoris causa in ingegneria meccanica all’Università di Perugia. Dall’intuizione vincente di Ricco si è poi passati all’ideazione, sviluppo e pre-industrializzazione, nel 1990, da parte del gruppo FIAT, allora costituito da Magneti Marelli, Centro Ricerche FIAT e Elasis. Nel 1994 l’industrializzazione effettiva venne gestita da Robert Bosch Gmbh, dietro pressione di Mercedes Benz, che successivamente si occupò anche della commercializzazione.
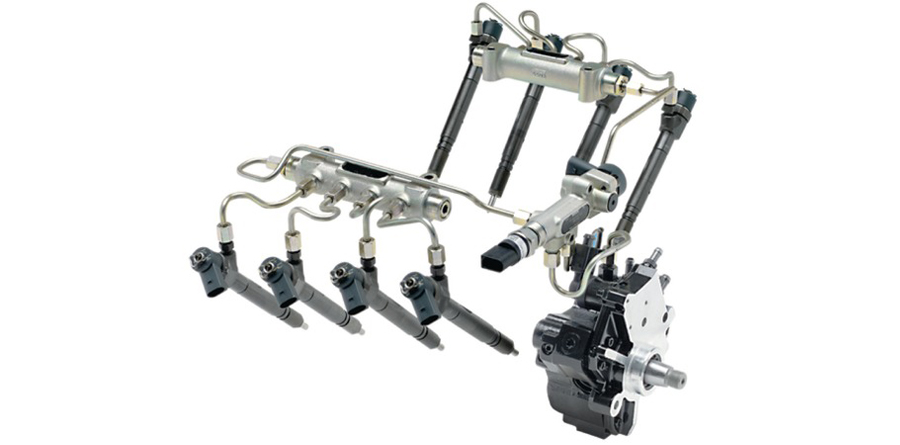
Applicazioni simili, ovvero funzionanti con lo stesso principio, risalgono però alle prime decadi del 900 in campo navale e ferroviario. Il principio del motore “Common Rail” ad iniezione diretta venne sviluppato dal Politecnico di Zurigo, sin dagli anni trenta ma non era conciliabile all’applicazione automobilistica. Uno dei primi esempi di motore Diesel Common Rail ad azionamento idraulico e poi conosciuto come Common Rail modificato, fu il Cooper-Bressemer GN-8 del 1942. Solo nel 1997, con l’Alfa Romeo 156 1.9 e 2.4 JTD si assiste alla sua prima applicazione in campo automobilistico. Per i primi due anni rimase esclusiva di FIAT, Alfa Romeo e Lancia e poi in seguito montato da quasi tutti i gruppi automobilistici. Fu solo successivamente, con la Bosch, che si assistette ad un notevole progresso tecnologico del motore, con la progressiva riduzione delle cilindrate, aumento delle prestazioni e una pressione massima d’iniezione di 1.350 bar; caratteristiche che hanno reso il Common Rail sempre più competitivo sul mercato, in precedenza dominato dal motore a benzina.
Ma tornando al 1997, il primo rail montato su una vettura si strutturava così: una pompa, indipendentemente dal regime di rotazione del motore, introduce gasolio all’interno di una condotta, il famoso rail, generando una pressione all’interno della stessa. Questa diviene un accumulatore idraulico, ovvero una riserva di combustibile in pressione pronto per essere iniettato nei cilindri. Il residuo, la parte di gasolio in eccesso, è rimandato al serbatoio dove si miscela con il gasolio a temperatura ambiente.
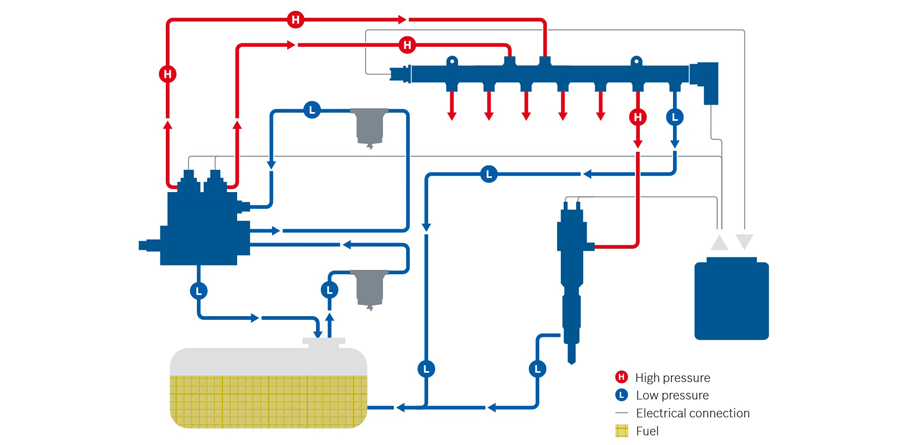
Nella sua prima applicazione automotive, questo ricircolo di gasolio caldo nel serbatoio causava problemi di affidabilità determinati all’innalzamento della temperatura globale nel circuito carburante, con pericoli di degradazione dei componenti di plastica ma il problema si risolse poi con una serpentina metallica di raffreddamento sotto la vettura.
Nel giugno 2008 fu presentata la seconda versione del Common Rail: il motore Multijet. Il concetto di base è suddividere l’iniezione in tre ravvicinate: pre, main e after mantenendo la possibilità di attuare le iniezioni pilot e post con più flessibilità temporale e raggiungendo una pressione massima d’iniezione di 1.600 bar. Così facendo la quantità di gasolio bruciata rimane la stessa ma la combustione è resa più graduale dall’aumento del numero delle iniezioni. Tra i vantaggi vi sono anche una maggiore silenziosità di funzionamento, riduzione delle emissioni e incremento delle prestazioni del 6-7%.
La terza generazione del Common Rail ha esordito nel 2013, con il motore Alfa Romeo JTDm2 per poi arrivare ad un ulteriore perfezionamento della tecnologia che ci ha condotti ai Common Rail di quarta generazione con gli iniettori piezoelettrici con pressione al ritorno ed il regolatore di pressione della pompa CP4, che vennero impiegati per la prima volta da Volkswagen nel 2008 sui nuovi motori 2.0TDI, 2.7TDI e 3.0TDI. Con questa nuova tecnologia aumenta ancora la pressione massima d’iniezione che raggiunge i 2.000 bar.
Soffermiamoci ora al componente per noi più importante del sistema, l’iniettore. L’inizio e la quantità di iniezione vengono impostati dalla centralina elettronica mediante un comando elettrico all’iniettore. Con il motore acceso e la pompa ad alta pressione in funzione si possono distinguere quattro diverse condizioni:
1 – iniettore chiuso (in presenza di alta pressione)
2 – apertura iniettore (inizio iniezione)
3 – iniettore completamente aperto
4 – chiusura dell’iniettore (fine iniezione)

Queste condizioni di esercizio vengono regolate mediante la distribuzione delle forze sui componenti dell’iniettore. Con il motore spento ed il Rail senza pressione l’iniettore rimane chiuso dalla molla. Per i motori ad iniezione diretta con Common Rail vengono usati polverizzatori a fori del tipo P con diametro dell’ago di 4 mm. Ne esistono di due tipi: polverizzatori a foro cieco (SAC) e a sede forata (VCO). I polverizzatori a foro cieco hanno i fori di spruzzo situati nel foro cieco e nelle versioni a punta tonda sono eseguiti meccanicamente o con un procedimento ad erosione elettrica, mentre nelle versioni a punta conica generalmente solo ad elettroerosione. Per ridurre le emissioni sono nati i polverizzatori a sede forata, in questo caso il foro di spruzzo inizia nella sede conica del corpo dell’iniettore e viene quasi completamente coperto dallo spillo quando l’iniettore stesso è chiuso. Per motivi di rigidità la punta ha una forma conica e i fori vengono generalmente eseguiti ad erosione elettrica.
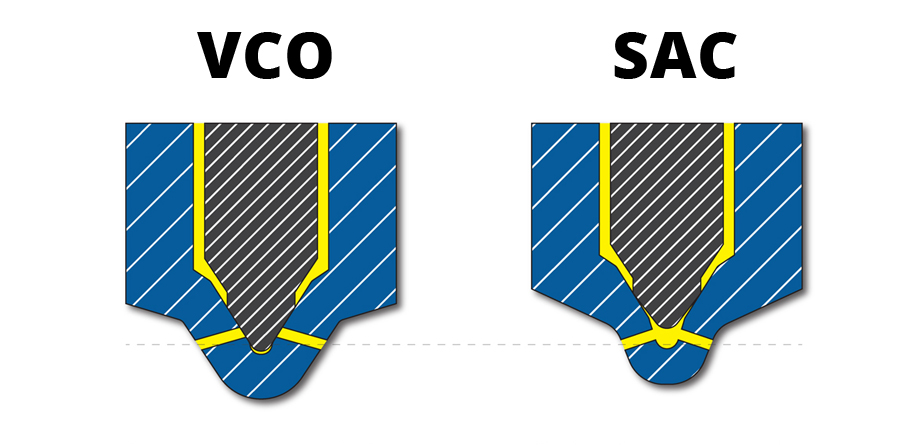
Il salto evolutivo-tecnologico del Common Rail ci ha stupito per la rapidità con la quale ha saputo migliorarsi e reinventarsi e possiamo solo aspettare di vedere in che altri modi ci stupirà in futuro.