HISTORY AND EVOLUTION OF COMMON RAIL SYSTEM
Although it became famous with its English name, Common Rail, the common rail diesel or common collector fuel supply system, whatever you want to call it, was invented by the Italian physicist Mario Ricco, who was awarded a master’s degree in honoris causa in mechanical engineering at the University of Perugia. On the basis of the winning intuition of Ricco, FIAT group, which was composed of Magneti Marelli, Centro Ricerche FIAT and Elasis in 1990, moved on to the conception, development and pre-industrialization of it. In 1994 the actual industrialization was managed by Robert Bosch Gmbh, under pressure from Mercedes Benz, who subsequently also dealt with marketing.
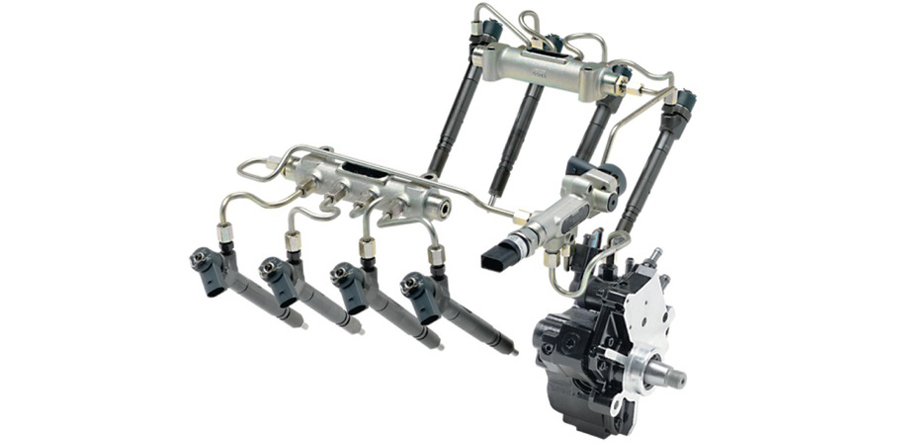
Similar applications, that is those ones operating according to the same principle, date back to the first decades of the 900s in the naval and railway fields. The principle of the “Common Rail” direct injection engine was developed by the Zurich Polytechnic since the 1930s but was not compatible with automotive application. One of the first examples of hydraulically driven Common Rail Diesel engine later known as a modified Common Rail was the 1942 Cooper-Bressemer GN-8. Only in 1997, with the Alfa Romeo 156 1.9 and 2.4 JTD, there was its first application in the automotive field. For the first two years it remained exclusive to FIAT, Alfa Romeo and Lancia and then later mounted by almost all the automotive groups. It was only later, with Bosch, that there was a remarkable technological progress of the engine, with the progressive reduction of displacements, increased performance and a maximum injection pressure of 1,350 bar; features that have made the Common Rail increasingly competitive on the market, previously dominated by the petrol engine.
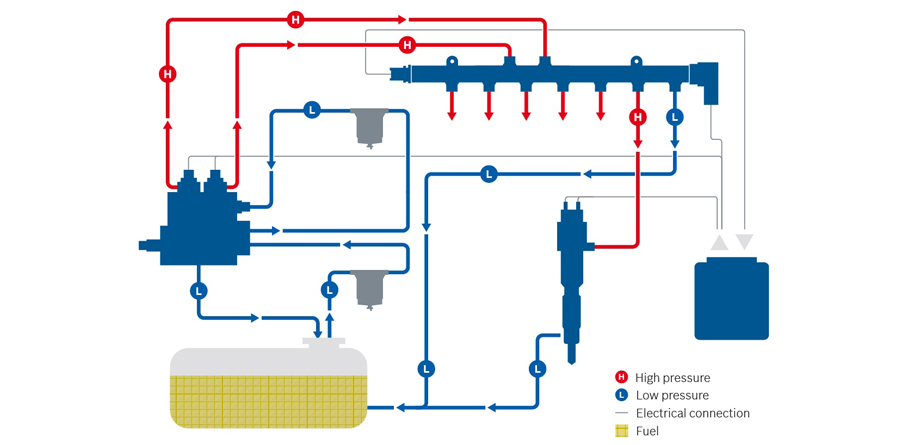
Back to 1997, the first rail mounted on a car was structured like this: a pump, regardless of the engine speed, introduces diesel into a duct, the famous rail, generating pressure inside it. This becomes a hydraulic accumulator, or a reserve of fuel under pressure ready to be injected into the cylinders. The residue, the excess diesel, is returned to the tank where it is mixed with diesel at room temperature. In its first automotive application, this recirculation of hot diesel fuel in the tank caused reliability problems determined by the raising of the global temperature in the fuel circuit, risks of degradation of the plastic components but the problem was then resolved by a metal cooling coil under the car.
In June 2008 the second version of the Common Rail was launched: the Multijet engine. The basic concept is to divide the injection into three closed actions: pre, main and after, assuring the chance of implementing the pilot and post injections with more temporal flexibility and reaching a maximum injection pressure of 1,600 bar. In this way the quantity of fuel burned remains the same but the combustion is more gradual by the increasing number of injections. Among the advantages there are less noise, reduced emissions and increased performance by 6-7 too.
The third generation of the Common Rail debuts in 2013, with the Alfa Romeo JTDm2 engine and then came to a further refinement of the technology that led us to the fourth generation Common Rail with piezoelectric injectors characterized by return pressure and the pressure regulator of the CP4 pump, which were used for the first time by Volkswagen in 2008 on the new 2.0TDI, 2.7TDI and 3.0TDI engines. This new technology has the maximum injection pressure increased up to 2,000 bar.
Let us now turn to the most important component of the system, the injector. The start and the injection quantity are set by the electronic control unit through an electric control to the injector. While the engine and the high-pressure pump run, four different conditions can be distinguished:
1 – closed injector (high pressure phase)
2 – injector opening (injection starting)
3 – fully open injector
4 – closure of the injector (injection ending)
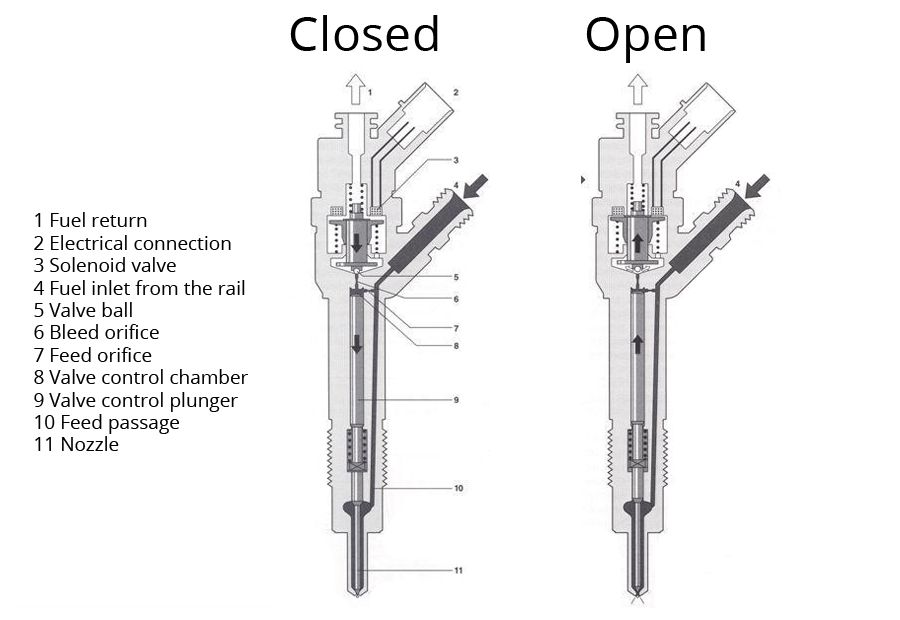
These operating phases are regulated by the distribution of forces on the injector components. With the engine off and the rail without pressure, the injector remains closed by the spring. In direct injection engines with Common Rail, P-type hole nozzles with a 4 mm diameter needle are used. There are two types: blind-hole SAC and perforated-seat VCO nozzles. Blind hole type (SAC) nozzles have spray holes located in the blind hole and in the round point versions they are mechanically or electrically eroded, while in the conical tip versions generally only with electroerosion. Perforated-seat nozzles (VCO) were born to reduce emissions, in this case the spray hole begins in the conical seat of the injector body and is almost completely covered by the pin when the injector is closed. For reasons of rigidity the tip has a conical shape and the holes are generally made by electric erosion.
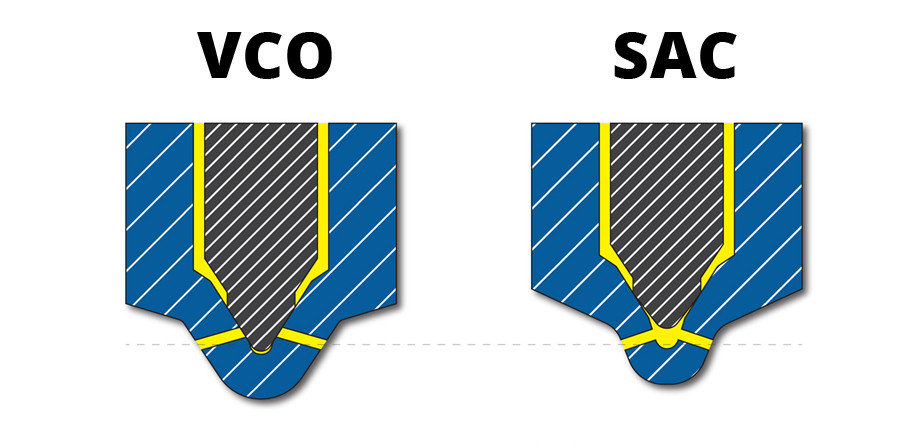
The evolutionary-technological leap of the Diesel Common Rail has surprised us due to the speed of improvement and reinvent itself. We can only wait for other ways it will surprise us.